Environmental Test Chambers for SAE J 2334 Surface vehicle standard
The SAE J2334 lab test procedure should be used when determining corrosion performance for a particular coating system, substrate, process, or design.
Since it is a field-correlated test, it can be used as a validation tool as well as a development tool. If corrosion mechanisms other than cosmetic or general corrosion are to be examined using this test, field correlation must be established.
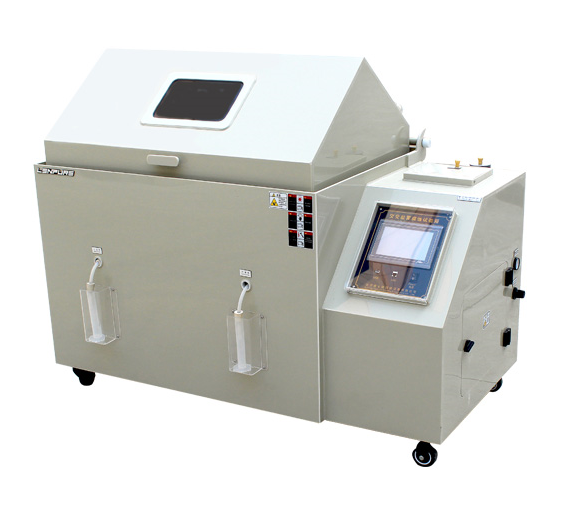
Definitions
Cosmetic Corrosion—Corrosion that occurs as a result of the breakdown or damage to a coating system.Typically, this type of corrosion does not impact function but does compromise appearance.
General Corrosion—Corrosion of a component that is typically bare (no organic coating). Corrosive attack is uniform in nature and distributed over “large” areas.
Scribe Creepback
Coating creepback resulting from corrosion and undercutting from the scribe line. Ascribe is a controlled simulated damage site designed to represent a scratch or chip.
Corrosion Coupons
Samples of bare metals, that are used to monitor and compare the corrosivity of laboratory corrosion tests in terms of mass-loss.
Test Controls
Components (i.e., test panels, coupons, parts, etc.) which have been previously tested and/or correlated. They can be used to control the test conduct and compare the test results (also assist in evaluating reproducibility and repeatability).
Equipment and Test Materials
Test Cabinets-Test cabinet(s) with the ability to obtain and maintain the following environmental conditions Reference SAE J1563. ASTM D 1735. and ASTM D 2247):
50℃±2℃ and 100% Relative Humidity-The 100% relative humidity wet-stage condition can be achieved by use of one of the three methods shown as follows. Whichever method is employed, test samples and controls are required to be visibly moist/wet.
Wet-bottom method according to ASTM D 2247- except that the temperature shall be 50℃± 2℃.
Water fog method according to ASTM D 1735. except that the collection rate is reduced from a range of 1.5 to 3 mL/h to 0.75 to 1.5 mL/h. The use of this method requires that the collection rates be documented.
Steam (vapor) generator method.
60℃±2℃and 50% Relative Humidity +5%. Additional equipment will be required to maintain the 50% relative humidity condition.
Air circulation must be sufficient to prevent temperature stratification and allow drying of test parts during the dry-off portion of the test cycle.Air circulation can be obtained through the use of a fan or forced air.
Salt Solution Application-The samples must be subject to an application of salt solution by use of one of the three methods shown as follows. Whichever method is employed, test samples and controls are required to be visibly moist/wet during the entire 15-minute interval of each test cycle.
0.5% Nacl
0.1% Cacl2
0.075% NaHCO3
Immersion Method-Test specimens are to be immersed in the salt solution for a 15-minute interval o each test cycle.
Spray Method-A periodic or continuous direct impingement spray of the salt solution over the 15-minute interval that ensures the test specimens are kept wet for the entire 15-minute interval. Avoid a high intensity (pressure) spray that may affect test results. (Note 5) Both direct solution displacement and atomized spray are suitable for this method.
Air Atomized Fog Method-Applications of the salt solution to the test specimens by a 15-minute exposure to atomized fog provided the fog collection rate is 2 to 4 mL/h instead of 1 to 2 mL/ (collection rate as defined in ASTM D 1735). The use of this method requires that the collection rates be documented.
Test Procedure
Test Cycle-The test cycle is outlined in Figure 1 (5 day/week - manual operation) and Figure 2 (7 day/week automatic operation). It consists of three basic stages:
1. Humid Stage-50 C and 100% humidity. 6 h in duration.
2. Salt Application Stage-15 min duration conducted at ambient conditions.
3. Dry Stage-60C and 50% RH, 17 h and 45 min in duration.
The test cycle is repeated daily. Fully automatic cabinets have the option of running during the weekends or programming in a dry stage soak for the weekends (typically it would be desired to run on weekends and holidays to complete the test sooner).
An exception to this rule would be if comparisons to other laboratories who do not have fully automatic capabilities is desired (for manual operations, the weekend exposure is typically maintained at dry stage conditions unless 7 day operations are available).
Total test duration and weekend conditions must be documented in the test results.
If two or more laboratories will be conducting tests on similar parts, it is recommended that a constant/common weekend condition be defined before testing begins.
Ramp time between the salt application stage (2) and dry stage (3) are part of the dry stage time. Similarly.amp time between the dry stage (3) and humid stage (1) are part of the humid stage. Ramp times should be documented for each test set-up.
For cosmetic corrosion evaluations of coatings susceptible to damage, test samples will be described prior to exposure (Reference ASTM D 1654). Scribe length should be a minimum of 50 mm. Scribe creepback measurements are to be taken at predetermined intervals depending on the level of corrosion resistance desired.
Scribe orientation, on the specimen, must be specified and documented (for typical flat panel specimens, it is recommended that panels be oriented 15 degrees from the vertical such that no one panel shadows another and that the scribe line be made in a diagonal across the panel face).
Test Duration-Typically, SAE J2334 is conducted for a minimum of 60 cycles when evaluating coated products. Longer durations may be required to observe performance differences in the heavier weight metallic precoats. Different test durations may be appropriate based on other materials. corrosion mechanisms of interest, or past history.
If you are still interested in any kind of environmental test chambers, and I'm pleased provide some of our details and project to you. That's more, at present we have more attractive price for you. Welcome for inquiry any time, I will reply asap!
If you want to know more information about climate chambers or our company, please feel free to contact sales@lenpure.com or visit http://www.lenpure.com/ .